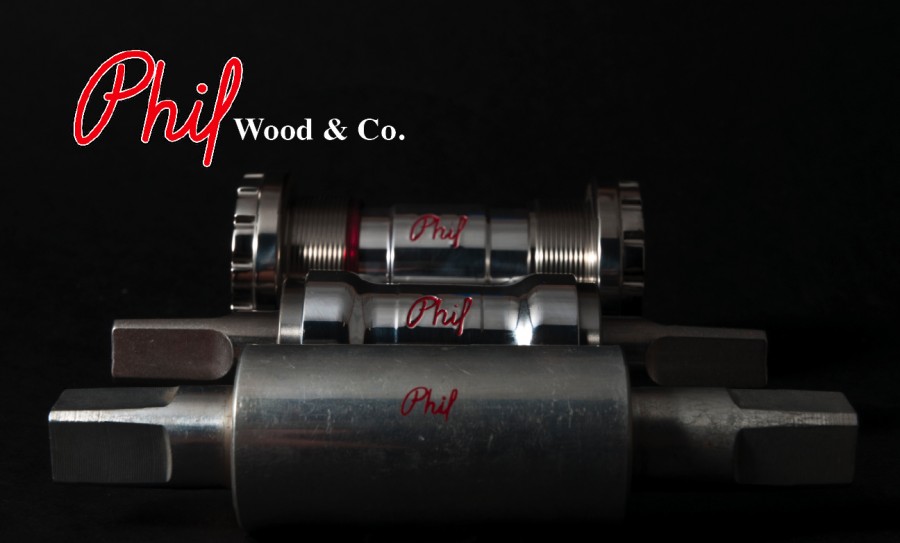
Taxonomy upgrade extras
San Jose, CA
Words by Garrett Enright
Phil Wood & Co was founded in 1971 in Los Gatos, California by Phil Wood, a mechanical engineer by trade. At this time Phil Wood & Co started producing the first modern cartridge-bearing hubs and square taper bottom brackets, the original hubs were a three-piece design. The aluminum flanges were pressed into a steel center shell and held together with a retaining compound. This three-piece shell design was changed in the early 80’s to a single aluminum shell with a steel insert. This new shell was the first to receive the polished finish Phil Wood & Co became well known for. In all of these earlier hubs the axle and bearings were pressed into the hub and held with a sleeve-retaining compound. In the mid 70s, Phil completed and began producing the spoke cutting and threading machine. In the early 80s Phil came up with the first pedal to be approved by the California Highway Patrol.
In 1990, Spence Wolf introduced Phil Wood to Peter Enright, who wanted to help Phil find a buyer for the company. After much thought, Peter along with other investors purchased the stock from the previous investors on April 1st 1991. At this time, Phil Wood took his leave, retired and moved to Baxter, Iowa. Once there, Phil spent most of his time helping to raise his great-granddaughter. Phil also found the time to write a textbook on differential calculus and a book on the theory of Turks head knot. He helped tutor local students, earning him an outstanding achievement award from the school board. As always, with every great man there is always a woman by his side to roll her eyes and give her unwavering support. For all of us who had the pleasure of meeting Lavada Wood it was clear that she was the support Phil needed to be as creative as he was. Lavada dedicated herself to Phil, her family, and Phil Wood & Co. Lavada would call Peter from time to time to see how everything was going and to give her support and let everyone know she was happy with the direction he was leading Phil Wood & Co.
Peter’s background and working carrier had helped prepare him to take the helm of Phil Wood & Co. In his previous corporate life he developed operating systems; computer interface cards; was immersed in metal structure and properties; traveled around the world starting up nuclear power plants; developed bio-medical devices; taught from the age of 20, in the engineering department at San Jose State University; and had a very successful engineering consulting business. One of the first tasks he set was to evaluate the current equipment at Phil Wood & Co. The equipment was made up of manual and NC (paper tape drive) mills and lathes. These machines had given their all in the first 20 years of the company and had deserved their retirement. He felt that there was a need for equipment that could both hold close consistent tolerances and be durable enough to function for at least 20 years. With this new goal, Phil Wood & Co. purchased its first CNC lathe. After the new CNC equipment had proven itself, it was felt that a new hub design could finally be put into production.
When working on the next generation hub design, Peter relied on ideals he held based on his work as an engineer and an avid cyclist; build something that will last a long time and improve the safety and enjoyment for the person using it. With this in mind, he fell back on the innovative design process he had picked up while working on power plants and began sketching out ideas on random scraps of paper, old envelopes, napkins, and every once in awhile a piece of drafting paper (only if it happened to be near him at the time). He called this new hub design FSA for “Field Serviceable Axle”. This design was a great improvement over older hub designs because now anyone with two 5mm hex wrenches could take their hub apart and service it if needed. Virtually all hub manufacturers have adopted this design in order to make servicing hubs much easier. Peter also improved on the bottom bracket design by using a more functional aluminum cartridge shell. In addition, he changed the stainless steel used in the spindle in order to increase its strength. In 1995, a titanium spindle was added to the bottom bracket line-up using a proprietary grade titanium Peter had analyzed during his days in the nuclear industry. The spoke cutting and threading machine was also refined. Small changes were made to make the machine operate more smoothly and make it easier to maintain. This refined spoke machine started with serial number 600 and has, over the last decade continued to receive additional material changes to improve its quality and longevity.
Along with these refinements in the standard product line, a passion for working on new products and custom parts began to grow. Phil Wood & Co worked with Rolf in developing his patented wheel design, collaborated with Dwan Shepard (President of Co-Motion) to establish a 145mm axle standard for tandem hubs; designed and made special hubs for wheelchair racing, Super Mileage vehicles, gravity vehicles, and Iditabikes.
Everyone at Phil Wood & Co. has a passion to always strive to improve the quality of our products without these changes being noticed. It has been said by some in the industry that our products never change. While this may appear to be correct based on the outward appearance of our products, this is not a whole truth. As improved materials become available to us and as our equipment becomes more sophisticated, we push ourselves to hold tighter tolerances and use these newly available materials to improve the quality of our products. In addition to machine and material improvements, the design tools we now use are much better than they have been in the past. Peter still occasionally sketches out new ideas on scraps of paper, but our head of R&D and lead engineer, Michael, helped make needed changes at the end of 2007. He moved from manually drawn blueprints to a 2D CAD system and then, the following year, to a 3D CAD system. By the end of 2009, a 3D printer was added to our R&D department to help us be more efficient in our design and prototype processes with minimal impact to our scheduled production runs. We feel that it is this constant desire to always improve our products that makes us unique. Today, Phil Wood & Co. makes over 3,000 different products. We all look forward to continuing to design and manufacture our products here in the USA to the high quality that Phil Wood & Co. is known for: Build it strong, keep it simple, make it work.